軋制技術及連軋自動化國家重點實驗室(簡稱RAL),前身是建于1950年代的東北工學院軋鋼實驗室,1995年通過國家驗收,成為了我國軋制技術及其自動化領域唯一的國家重點實驗室。實驗室自1995年開放運行以來,致力于使我國鋼鐵行業成為全球鋼鐵行業的領跑者,推動了我國鋼鐵行業“由大到強”。
RAL面向國家重大戰略需求,面向經濟社會主戰場,面向世界科技發展前沿,面向人民生命健康,結合行業特點與學科優勢,圍繞鋼鐵行業綠色化、高質化、數字化轉型發展戰略需求,針對國家對“產品高質化、工藝綠色化、裝備智能化”的重大任務,在低碳冶煉與全流程低碳加工、高端特種金屬材料和先進鋼鐵材料創新與研發、鋼鐵行業智能化和數字化轉型發展、關鍵冶金工藝裝備等方面,引領了我國鋼鐵行業發展和技術革新。
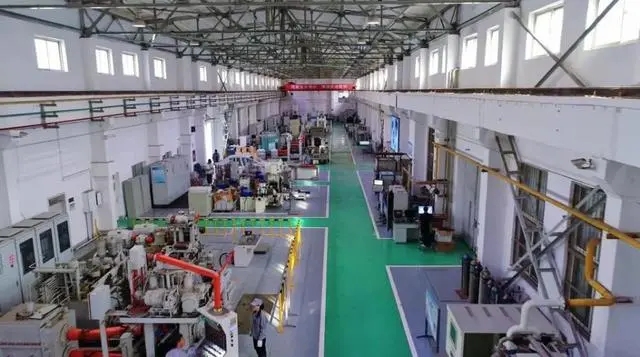
軋制技術及連軋自動化國家重點實驗室
在先進鋼鐵材料原始創新和高端金屬材料制備技術突破方面,“超級鋼”填補國內外空白,中高錳海洋平臺用鋼、船用高止裂韌度特厚鋼板、2000MPa高強韌汽車鋼、1900MPa高強韌彈簧鋼、節約型高性能LNG儲罐用鋼、高韌性Al-Si鍍層等高端金屬材料研發解決了一系列行業“卡脖子”難題;在鋼鐵材料組織精準柔性調控和高端超薄、超寬、超厚鋼板熱處理領域,超快冷和輥式淬火成套工藝裝備打破國外技術壟斷,促進了重大冶金裝備國產化進程,滿足了國家重點領域對高等級鋼板的急需;基于流程工業特點,率先開發出金屬材料生產全流程的系列動態數字孿生模型,構建了多工序全流程協調優化的CPS系統與面向未來的鋼鐵智能制造架構,成為鋼鐵全流程智能制造的引領者。
1999—2005年間,王國棟院士開發出我國第一塊超級鋼。2002年,東北大學與寶鋼集團有限公司、第一汽車集團公司等企業合作,通過軋制與冷卻條件的控制,將屈服強度200MPa級普碳鋼升級為屈服強度400MPa級的超級鋼,成功應用于汽車制造等行業,實現了我國超級鋼的工業生產,在國際上連創4個第一:第一次在實驗室條件下得到了原型鋼樣品;第一次得到鋼鐵工業生產的工藝窗口;第一次在工業生產條件下軋制出超級鋼;第一次將超級鋼應用于汽車制造。這標志著我國超級鋼的開發應用完成了由跟跑、并跑到領跑的跨越,走到了國際前列。2004年,該項目獲得國家科技進步一等獎。目前,這一研究成果被應用于寶鋼、鞍鋼等企業,已批量工業生產超級鋼數百萬噸,產生了巨大的經濟效益和社會效益。
近年來,實驗室積極組織、承擔各類國家重大、重點項目。主持了8項、承擔多項國家重點研發計劃項目,主持參與多項863計劃項目、973計劃項目、國家自然科學基金項目、國家攻關計劃項目等。主持橫向科研項目千余項,科研項目轉化合同金額近34億元,解決了大量行業和企業急需的關鍵共性技術難題和前沿技術問題。相繼獲得國家級科技獎勵15項,其中一等獎3項,二等獎12項,省部級科技獎勵167項;發表研究論文5500余篇;出版論著100余部;獲得發明專利760余項,其中國際專利11項。
RAL已經成為我國先進鋼鐵材料研發和軋制技術的基礎研究與應用基礎研究基地、鋼鐵材料研發與軋制技術成果的輻射基地、高層次人才的培養基地和學術交流基地,為我國鋼鐵行業的創新發展與技術進步做出了突出貢獻。